The Quintessential Supply Chain Bottleneck – Counting the Cost of the Ever Given
Forget three French hens – just when we thought things couldn’t get any more chaotic in the supply chain world this happened. How did the Suez Canal blockage affect you and your organisation?
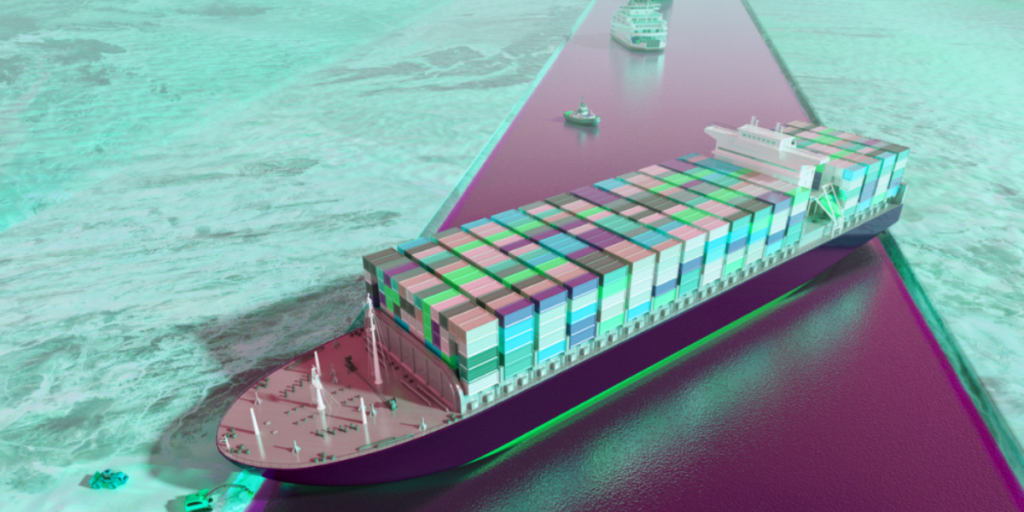
Operating uninterrupted for the better part of half a century, the case of Suez Canal vs the wedged Ever Given should prompt organisations to ask some tough questions about agility and risk.
Since its construction in the late 1850s, the Suez Canal has been a key shipping route between the Mediterranean and Red Seas. It is one of the busiest and most important trade routes in the world, accounting for approximately 12 per cent of global trade. Goods shipping daily along the Canal are valued at an estimated $9 billion. It is also perhaps the most obvious potential bottleneck in waiting.
And bottleneck it did on March 23. The Ever Given – a 400 metre-long, 220,000-tonne container ship – ran aground, officially closing the Canal for six days. The backlog of ships was only starting to be cleared by the Suez Canal Authority as of March 30.
The costs associated with the delays rapidly reached eye-watering levels. Egypt alone lost revenue of $12-14 million per day. However, even as the shipping traffic was beginning to move more freely again, global supply chains were only just starting to count the cost of the disruption.
Months of Supply Chain Disruption Ahead
When the Canal was reopened, there were an estimated 350-400 ships in the queue. Their cargos ranged from liquified natural gas and Crude oil, to global commodities such as coffee beans and Amazon deliveries. Due to the sheer volume of goods traversing the waterways, experts have warned that supply chains could be disrupted for months to come.
Ships are continuing journeys without firm arrival dates. At the same time, ports are facing a surge in demand due to delayed ships all arriving at once. In addition, many carriers were also carting empty shipping containers back to be refilled for their next journeys. These delayed key exports from China and India have the potential to exacerbate an already-existing issue in maritime logistics as a result of COVID-19.
Experts have warned that supply chains could be disrupted for months to come
Many organisations are already being hit with increasingly expensive bills due to both the delays and limited alternative transportation options. Renting other vessels, shipping via alternative routes or using air freight all come with a high price tag. This is owing to increasing demand or fuel costs due to longer journeys. The impact will be felt most keenly in factories, distribution centres and warehouses that usually rely on holding a minimum level of stock or inventory.
Flexibility and Risk Management
Costs are likely to be the most pressing concern to organisations in the short and medium term. The longer-term outcomes of this situation, however, are linked to the agility and flexibility of supply chains. Organisational risk management and contingency planning also play a role. The global impact of events, including COVID-19 and the Suez Canal, have exposed the need for strong and stable supply chains. And they need to demonstrate flexibility in the face of an unexpected crisis.
In recent years, organisations have used service outsourcing and procurement in low-cost countries to reduce expenses. Problematically, this has added layers of complexity and reduced flexibility in supply chains. According to maritime expert Captain Andrew Kinsey, organisations affected by the Suez Canal blockage who are searching for lower costs have left themselves at the mercy of larger shippers. The priorities and economies of scale of these larger shippers could be vastly different to those of their customers.
Organisations will need to critically examine their supply chains to understand how to avoid future issues. They must then embed new risk management policies and contingency planning based on their findings. Strategies may include onshoring, reducing or mitigating bottlenecks and choke points, or cultivating new sourcing opportunities to reduce risk.
Key to a supply chain’s agility is ensuring multiple transportation options are available. Onshoring or reduced reliance on Just-in-Time are just two. Supply chain expert Tom Fairbairn (Distinguished Engineer at Solace) believes organisations need to review their operational strategies in line with technological advancements.
Fairbairn argues: “Digitised supply chains and technology help organisations adapt to disruptions faster and better, reducing the cost impact and downstream impact on customers.”
It’s a strategy more organisations may be considering in light of recent events.