How the Baltimore Bridge Collapse Impacts The Supply Chain
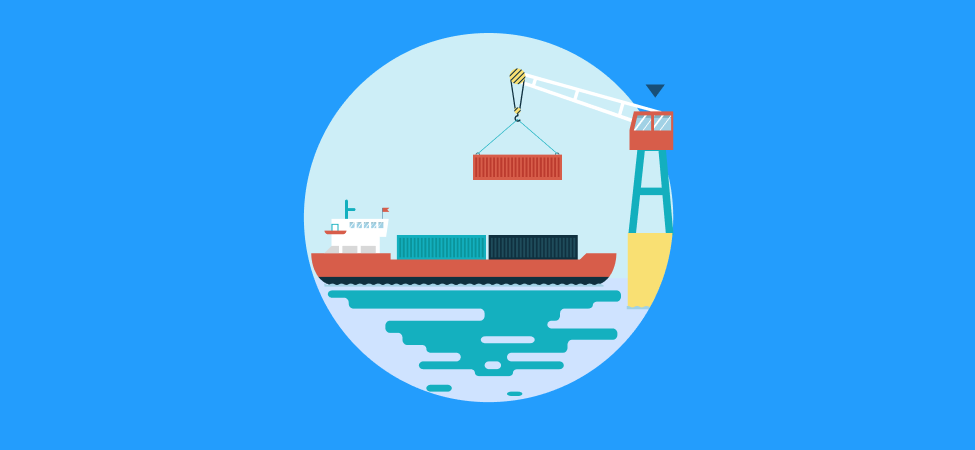
Just two weeks after the Francis Scott Key Bridge in Baltimore, Maryland, collapsed after a cargo ship ran into it, vessels are moving through temporary channels, restoring service to this active port.
Supply chain experts predict that shippers will experience significant delays and rerouting for inbound shipments. Logistics and supply chain managers should expect longer lead times and potential price hikes in procurement of raw materials and inventory.
However, with lessons learned from the Covid pandemic supply chain disruptions, companies may be better positioned to withstand this challenge.
Deep Impact
More than 30 vessels have navigated via temporary channels on the Patapsco River since the Dali slammed into the bridge on March 26, killing six workers. The accident stranded 11 ships at the Maryland port, costing one roll-on/roll-off carrier as much as $10 million. Salvage crews are removing containers from the vessel’s deck, clearing the way to remove the steel sections of the bridge laying across the ship’s bow.
The Port of Baltimore is one of the 10 largest ports in the U.S. in terms of the dollar value of cargo handled. It is a critical hub for steel, aluminium, sugar, vehicles, agricultural equipment, and containers. Typically, 30-40 container vessels call the Port of Baltimore weekly, unloading or loading some 21,000 containers. These containers must now be diverted to nearby ports.
Numerous industries are especially dependent on the port of Baltimore, which ranks first among U.S. ports for the volume of automobiles and light trucks, roll on/roll off heavy farm and construction machinery, gypsum, and sugar. The cargo diversions will have a ripple effect on vessel schedules and strained labour and handling capacities at other ports such as Philadelphia and Norfolk, leading to congestion and delays that could last months.
Time-sensitive and perishable products could be particularly affected. High-value cargo may be rerouted to air freight carriers to meet tight deadlines.
Recovery Underway
The Biden Administration hopes to restore normal service to the port of Baltimore by May 31. In the meantime, the government has granted $8 million to double the auto handling capacity at one of the port’s unaffected automobile terminals.
At the same time, the Federal Motor Carrier Safety Administration granted a waiver of two additional hours of service to allow Baltimore-based truck drivers to move cargo to and from the port of Norfolk.
Trucks in the area are rerouting through the Fort McHenry Tunnel on Interstate 95, which adds 9 to 10 miles compared to the bridge route, which takes on average 11 minutes longer in travel time, according to fleet telematics provider Trimble. However, some trucks could experience congestion delays of an hour or more.
One uncertainty for shippers with cargo on the Dali is whether they will be financially responsible for expenses related to the emergency under a shipping regulation called General Average.
Harsh Lessons Learned
Learning from the painful lessons of the pandemic, many companies have taken steps to improve their supply chain procedures.
The Digital Payments: Modernising Procurement Processes report from PYMNTS Intelligence found that manufacturers and retailers focused on logistics and supply chain improvements as a top priority. In the survey of 500 CFOs, 55% of manufacturers and 54% of retailers reported investing heavily in their procurement systems and upgrading their logistics and supply chain functions.
One target area is supplier data systems, such as real-time inventory information and supply chain analytics. These systems help businesses plan and forecast inventory needs while providing visibility to broaden supply chains as needed. The early days of the pandemic revealed deficiencies in these capabilities became very apparent.
The survey segmented 41% of retailers and 39% of manufacturers as investing in analytical systems and upgrading supplier data. Nearly 12% of healthcare companies and 13% of finance and insurance businesses were making moves.
As the Port of Baltimore recovers, supply chain disruptions are in force around the world, including geopolitical unrest in the Red Sea and low water conditions in the Panama Canal. Supply chain resiliency is a journey, not a destination.
Companies that learned the hard lessons of the pandemic may be better prepared with system upgrades that facilitate smoother procurement and supply chain efficiencies.